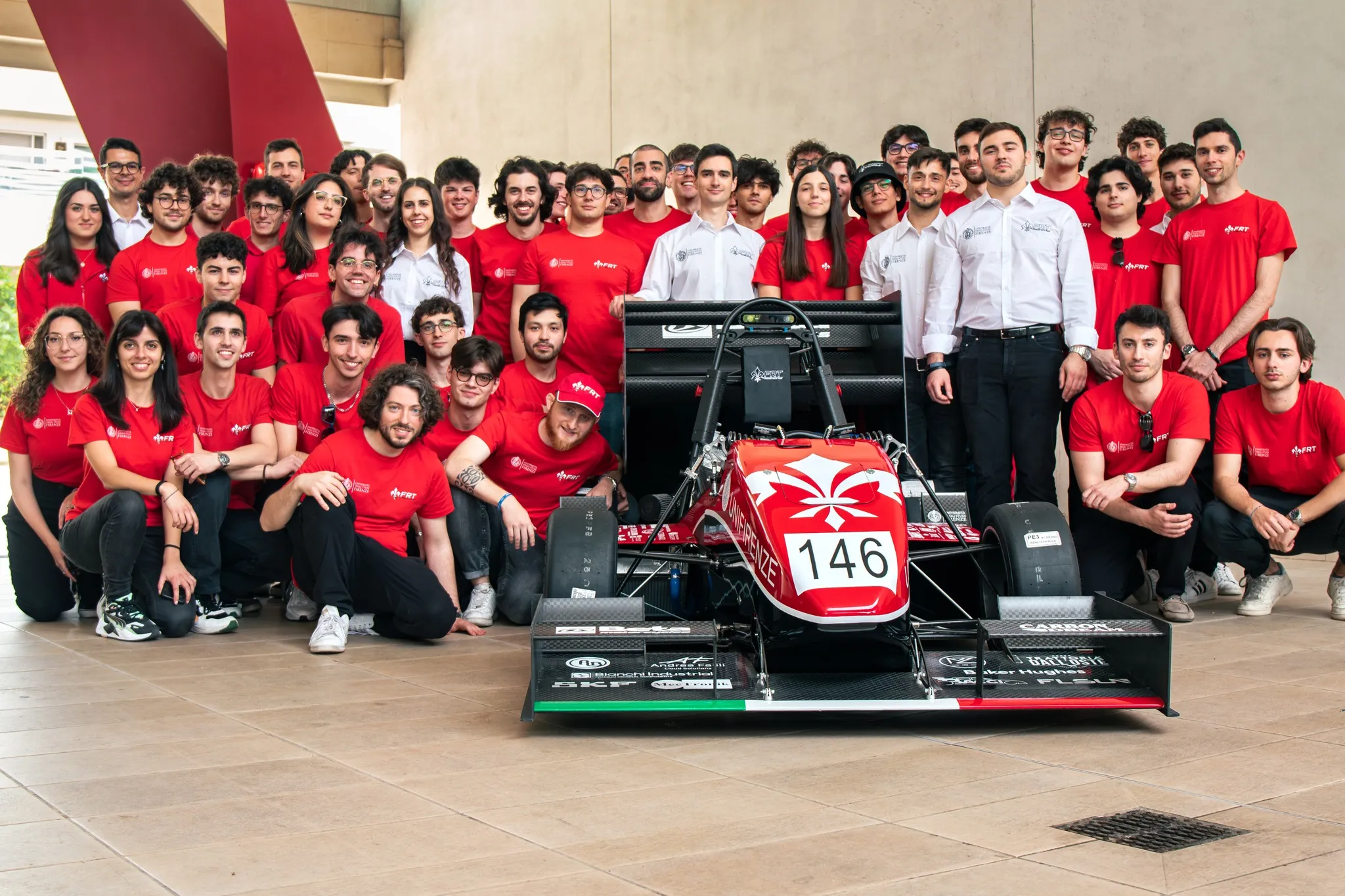
The soul of the project
We are excited to introduce the members of the Firenze Race Team, consisting of about 70 students, each bringing a unique set of skills and extensive experience in their field. The team members come primarily from the School of Engineering at the University of Florence, but also include students from other schools.
Discover our Team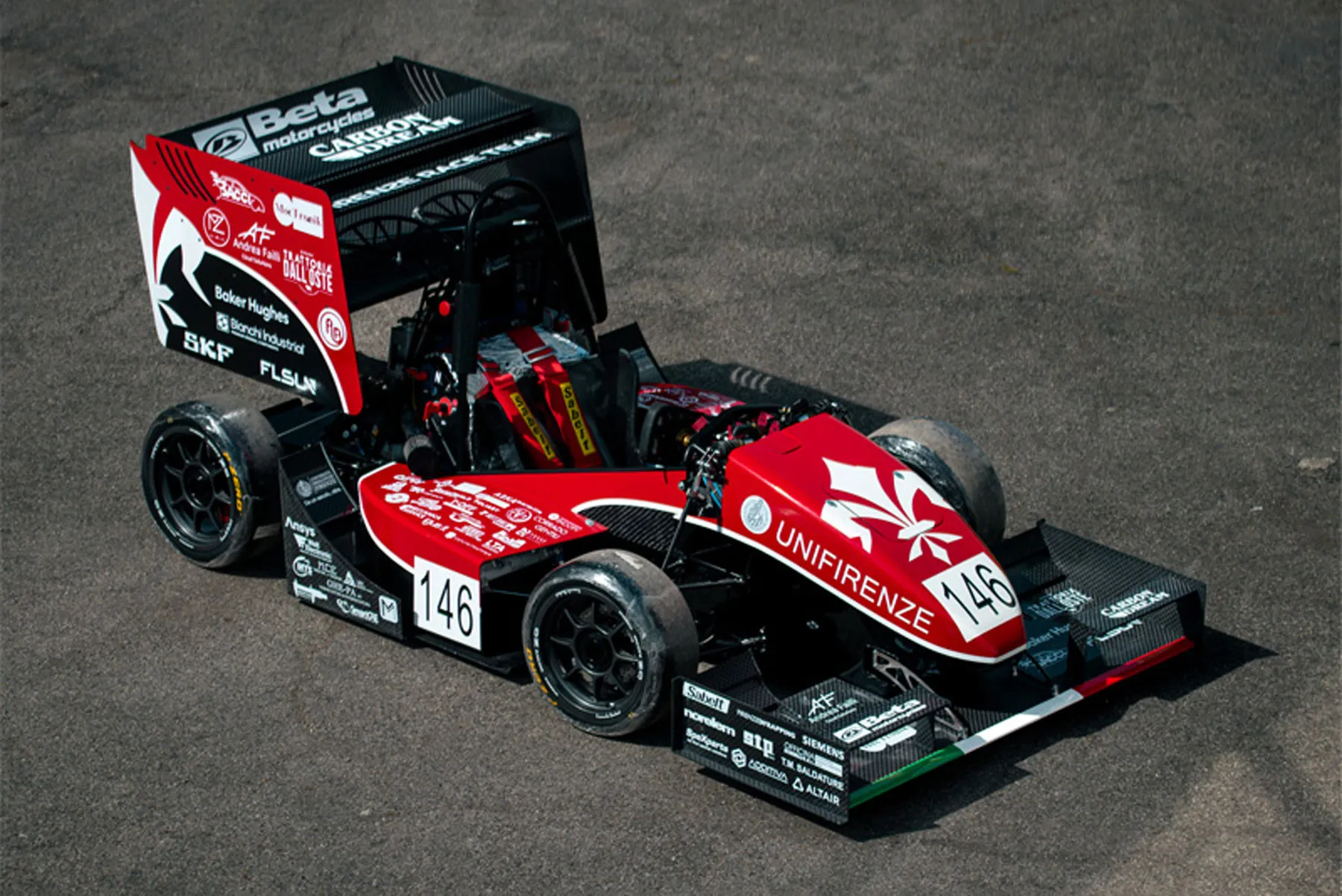
Our creations
From the earliest inventions to the most technologically advanced, each car represents a chapter in our story of innovation and passion for engineering. Get ready to explore our journey through the world of racing, where each vehicle has made its mark and contributed to defining our competitive spirit and dedication to engineering.
Discover our CarsThe FR-25 is an evolution of its predecessor, retaining the autonomous driving system that enables fully driverless operation. The main innovations focus on optimizing aerodynamic load through a redesigned bodywork and reworked front and rear wings, with particular emphasis on the underbody and the removal of the sidepods. These changes have significantly improved the overall efficiency of airflow management. In parallel, a newly designed cooling system has been introduced, featuring two radiators positioned symmetrically on either side of the vehicle. This setup integrates seamlessly with the updated aerodynamic geometry. To celebrate the 25th anniversary of the team, the FR-25 features a special livery inspired by the color scheme of the very first car built by the Firenze Race Team, blending innovation and tradition in a single iconic design.
Discover the FR-25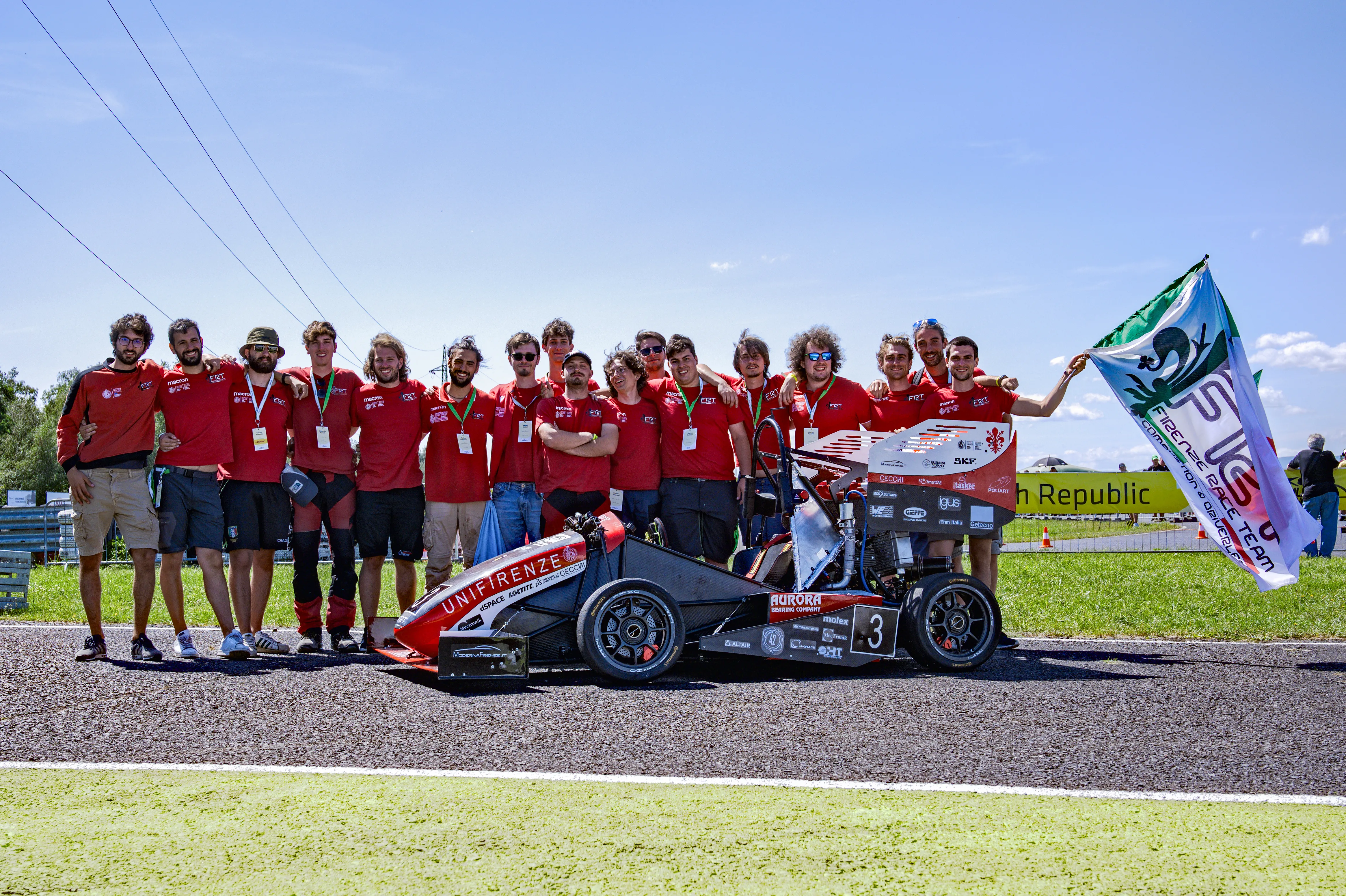
The highlights
Since its creation, the Firenze Race Team has always been a point of reference for all students at the University of Florence who are passionate about motorsport, and beyond. Over time, the team has made a name for itself both nationally and internationally through the various competitions and events organised mainly in our territory. All this has led to great collaborations with world-renowned partners operating in the motorsport sector.
Discover FRT Events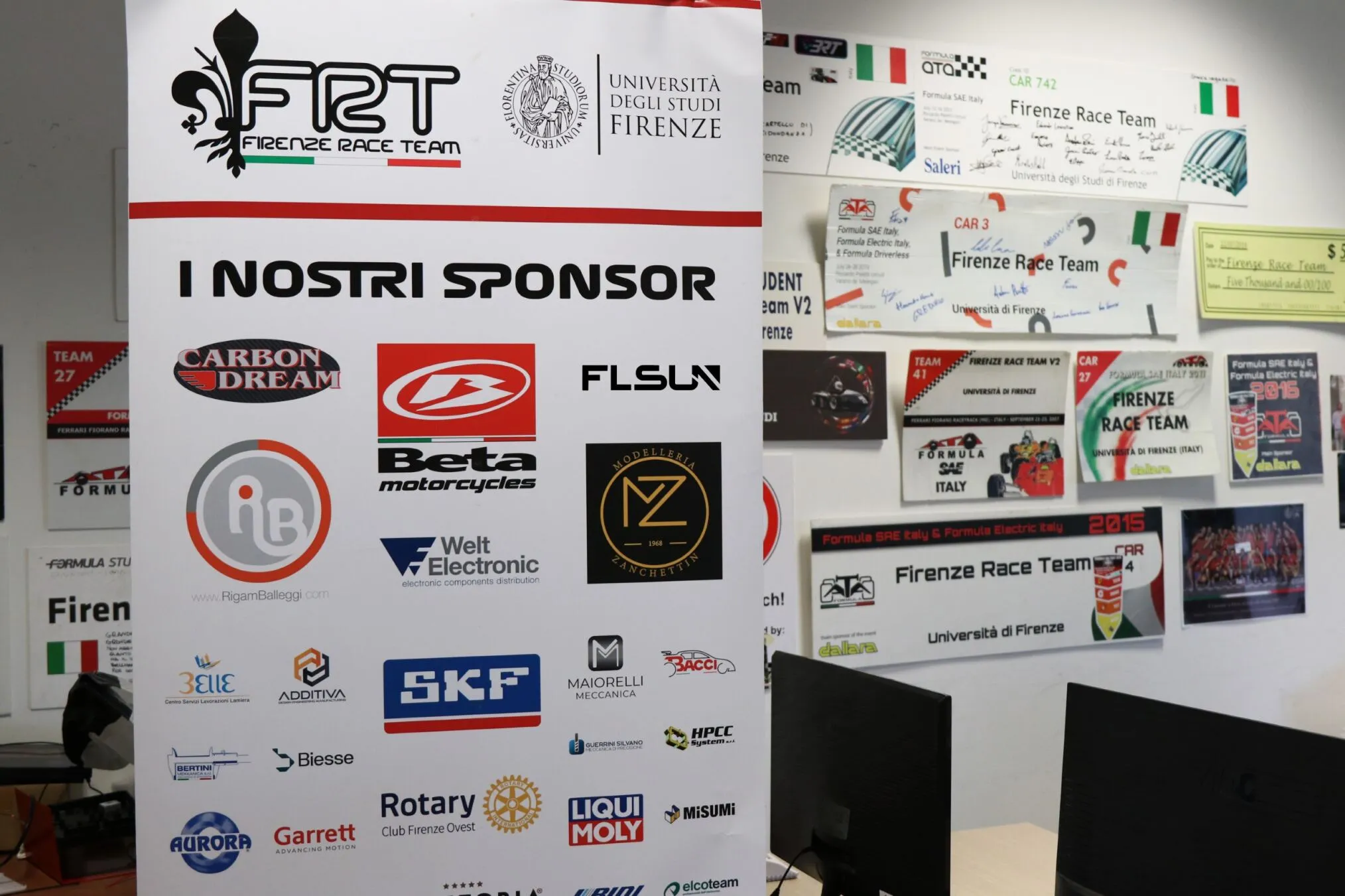
Our supporters
Collaboration is very important in the world of Formula Student, as the budget is small, but there is a lot of work to be done. That's why every kind of help is essential in this sector, and the Firenze Race Team can count on the support of more than 100 partners who help the team to build a car that is able to face all the tests in the competitions.
Discover our Partners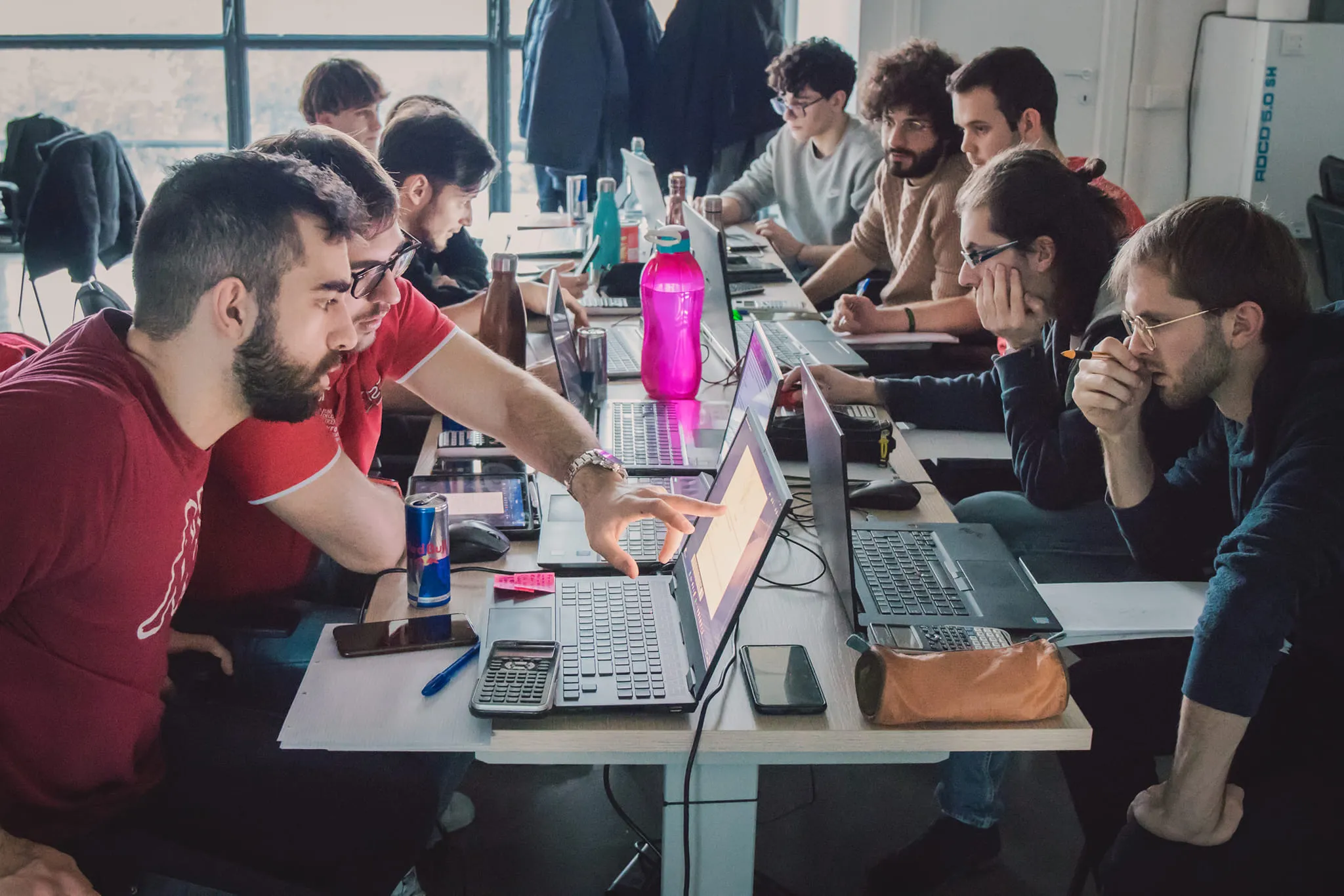
Activities and partnerships
Il Firenze Race Team TODO Lorem ipsum dolor sit amet, consectetur adipiscing elit, sed do eiusmod tempor incididunt ut labore et dolore magna aliqua. Ut enim ad minim veniam, quis nostrud exercitation ullamco laboris nisi ut aliquip ex ea commodo consequat. Lorem ipsum dolor sit amet.
Discover FRT Activities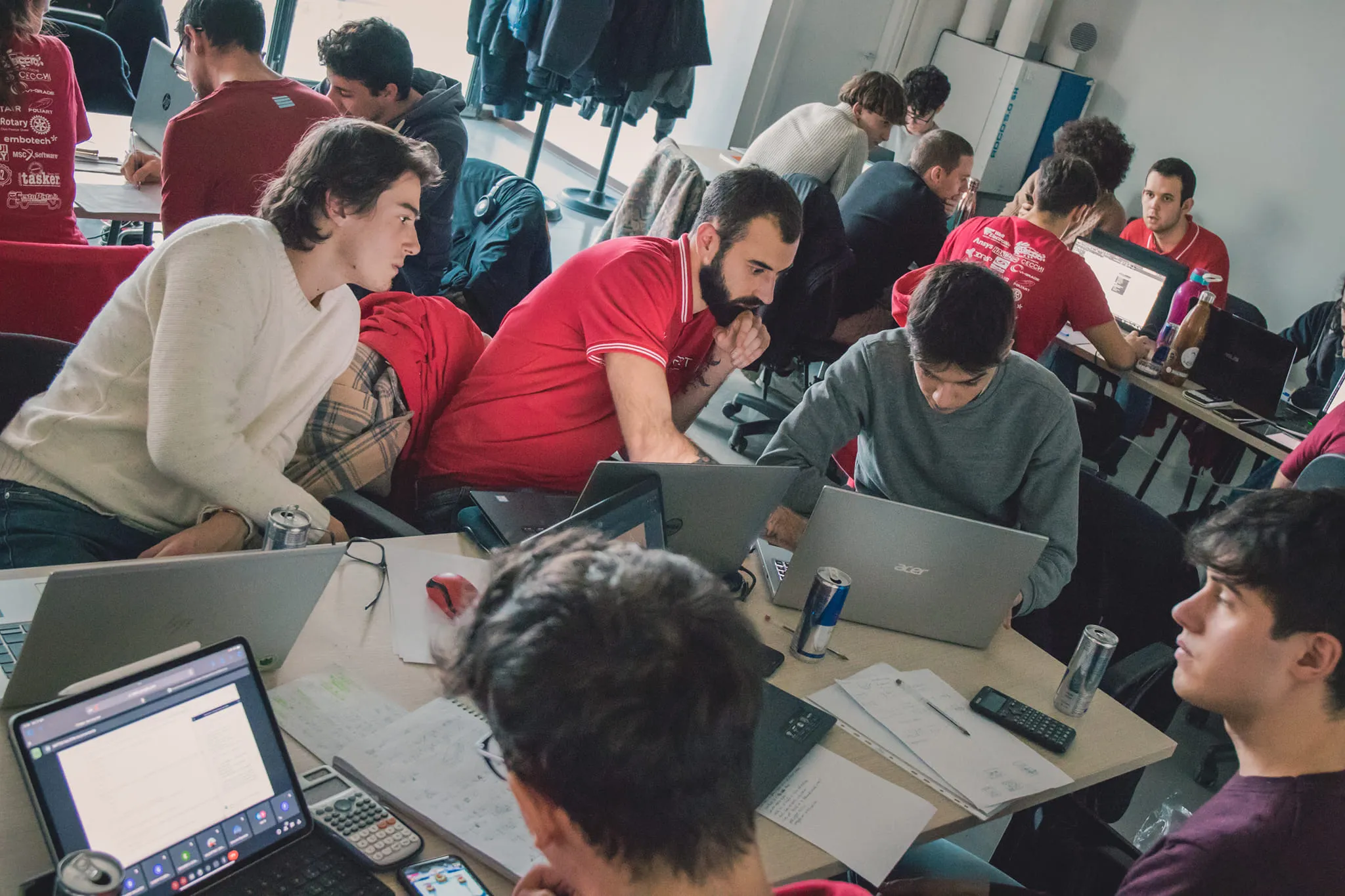
Press releases
Il Firenze Race Team TODO Lorem ipsum dolor sit amet, consectetur adipiscing elit, sed do eiusmod tempor incididunt ut labore et dolore magna aliqua. Ut enim ad minim veniam, quis nostrud exercitation ullamco laboris nisi ut aliquip ex ea commodo consequat. Lorem ipsum dolor sit amet.
View Press ReleasesFRT History
Accomplished results
2024
Formula SAE Italy, Varano de’ Melegari (IT) – Class 1D
4th place – Overall ranking
2nd place – Business Event
6th place – Design Event
6th place – Cost Event
Formula Student East, Zalaegerszeg (HU) - Class 1C
5th place – Overall ranking
4th place – Business Event
4th place – Design Event
5th place – Cost Event
2023
Formula SAE Italy, Varano de’ Melegari (IT) – Class 1
3rd place - Cost Report
2022
Formula SAE Italy, Varano de’ Melegari (IT) – Class 3
1st place - Overall standings
2021
Formula Student Czech Republic, Most (CZ) – Class 1
6th place - Cost Report
6th place - Engineering Design
2019
Fomula SAE Italy, Varano de’ Melegari (IT) – Class 1
3rd Place - Cost Report
2017
Formula SAE, Hockenheim (D) – CLASS 1 Driverless
12th place - Overall ranking
First team in the world to participate in a Formula SAE event with an autonomous car powered by a combustion engine
Fomula SAE Italy, Varano de’ Melegari (IT) – Class 3
2nd Place - Overall standings
2nd Place - Design Presentation
1st Place - Cost Analysis
2016
Fomula SAE Italy, Varano de’ Melegari (IT) – Class 1
3rd Place - Overall standings
4th Place - Design presentation
1st Place - Cost analysis
3rd Place - Business presentation
First Italian Team
"ZF TRW-Driving Safety to Safely Drive" Award
2015
Fomula SAE Italy, Varano de’ Melegari (IT) – Class 1
7th place - Overall standings
5th place - Design Presentation
5th place - Cost Analysis
"Best use of active frame systems" award.
2013
Formula Student, Silverstone (UK) – Class 2
2nd place - Overall standings
1st place - Cost Analysis
2011
Fomula SAE Italy, Varano de’ Melegari (IT) – Class 1
1st place - Business Presentation
1st place - Cost Analysis
2010
Fomula SAE Italy, Varano de’ Melegari (IT) – Class 1
2nd place - Business Presentation
2008
Formula SAE Italy, Fiorano (IT) – Class 1
1st place - Cost Analysis
"Schaffler Group" Award - 'The best selection of bearings and design'
Formula Student, Silverstone (UK) – Class 1
1st place - Cost Analysis
2007
Formula SAE West, Fontana (USA) - Class 1
First Italian team to participate in a race in the USA
Formula SAE Italy, Fiorano (IT) – Class 1
1st place - Cost Analysis
Most Friendly Team Award
2006
Formula SAE Italy, Balocco (IT) – Class 3
1st place - Overall standings
2005
Formula SAE Italy, Balocco (IT) – Class 1
2nd place - Overall standings
1st place - Autocross
2nd place - Skidpad
2nd place - Endurance
"MSC Software" award - 'Best virtual development team'
"Automobilismo" magazine award - 'To the most innovative project'
2004
Formula Student, Leicester (UK) – Class 1/(200)
4th place - Overall standings Class 1 + Class 1/(200)
2nd place - Overall standings Class 1/(200)
1st place - Design Event Class 1/(200)
3rd place - SolidWorks 3D Design & Analysis Awards
2003
Formula Student, Leicester (UK) – Class 1
15th Place - Overall standings
Best Rookie Team Award
2002
Formula Student, Leicester (UK) – Class 3
2nd place - Overall standings
1st place - Design Event
1st place - Business Presentation
First ever participation of an Italian team in an F-SAE Series event
2000
Firenze Race Team Foundation
Firenze Race Team Foundation